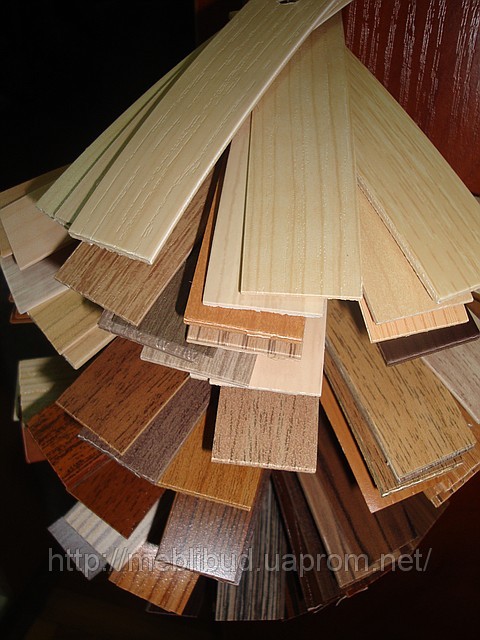
ПВХ Кромочные материалы
Кромочные материалы. Классификация и история (часть 1)
2009.12.11
Кромочные материалы - это то, что наши мебельщики, часто неискушенные в тонкостях профессиональной терминологии, называют как придется: кромкой, полосой, лентой, кантом, а кто и торцевой наклейкой, или даже "торцевой зашлепкой".Но это вполне объяснимо - специальной литературы и учебников, в которых была бы приведена классификация кромочных материалов и соответствующие определения, просто не существует.Продавцы фирм, реализующих кромочные материалы, к сожалению тоже не могут дать необходимые разъяснения покупателям, поскольку сами пользуются неизвестно откуда появившимися понятиями вроде "кромка-меламин" или "кант врезной".
Облицовывание как часть отделки
Россия, много столетий находившаяся под влиянием Востока, где мебель никогда не была главным предметом интерьеров, не стала прародительницей ни одного из мебельных стилей. Европейская мебель и технологии ее производства пришли к нам стараниями царя Петра I лишь в начале XVIII века.
С ними появились и новые названия инструмента и оборудования. Так, даже такие, казалось бы, "исконно русские" слова, как рубанок и фанера, произошли от немецкого Raubank и шведского Fanret. И процесс заимствования продолжается до сего дня.
Но пока сохраняется такое русское понятие, как отделка изделий, под которой в широком смысле понимается вся совокупность способов обработки поверхности древесины и древесных материалов для защиты от воздействия окружающей среды и улучшения внешнего вида. Отделка изделий осуществляется путем облицовывания, отделки лакокрасочными материалами, нанесения резьбы, инкрустации, пирографии (выжигания), пиротипии, термопечати и т. п. Однако в современном значении под отделкой чаще всего понимают только создание на поверхности деталей и изделий защитных, декоративных и защитно-декоративных покрытий с помощью лакокрасочных материалов, в общем случае разделяемых на прозрачные и непрозрачные (укрывистые), а облицовывание как бы выделилось в отдельный вид технологии.
Облицовывание - общее наименование процессов наклеивания какого-либо тонкого материала на поверхность заготовки, детали или изделия с целью облагораживания поверхности подложки, придания ей нового вида. Причем правильным является термин "облицовывание", а облицовкой называется то, чем облицована поверхность.
Мебель, изготовленная из цельной древесины недорогих хвойных и лиственных пород, без облицовки на поверхности по-русски называлась белодеревной, а облицованная - оклейной.
Причем процесс облицовывания поверхностей тонким слоем древесины более ценных пород называется фанерованием - от слова "фанера", и никак не шпонированием, поскольку шпон - прирезанный в размер лист лущеной фанеры, который изначально использовался для получения фанеры клееной, и лишь потом это название перешло на листы прирезанной строганой фанеры.
В любом случае, отечественные линии МФП и МФК, разрабатывавшиеся еще до появления у нас синтетических облицовочных материалов, назывались соответственно линией фанерования пластей и линией фанерования кромок.
Кромка, торец или кант?
К сожалению, большинство наших мебельщиков сегодня не только не читает учебников, но и не знает государственных стандартов, в которых достаточно четко изложено, что такое пласть, кромка, ребро и торец. Ярким свидетельством может служить содержание сайтов мебельных предприятий в Интернете, где кромка называется, например, ребром, торцом или, хуже того, кантом.
Вместе с тем, еще в школе мы учили, что плоская часть поверхности геометрического тела называется гранью, а тело, поверхность которого образована пересечением нескольких плоскостей, - многогранником. Один из многогранников - параллелепипед, форму которого имеет большинство заготовок и деталей в производстве мебели.
К ним относятся имеющие шесть граней четырехбитные брусья, доски, плиты, прямолинейные бруски и большинство прямоугольных щитовых деталей.
При этом пластью называется каждая из двух наиболее широких сторон (граней) любой плоской заготовки, детали или изделия, например, бруска, доски и т. д., а также и любого матраца. Любая продольная поверхность заготовки с квадратным сечением тоже называется пластью. А вот узкие продольные и поперечные грани щитовых и брусковых деталей, а также плит, называются кромкой. Так же называется и продольный край полотна какой-либо ткани или характерная узкая полоса, идущая вдоль этого края.
Торец - поверхность поперечного разреза, среза бревна, бруса, бруска, а также вообще поперечная грань какой-либо достаточно узкой длинной детали, концевое поперечное сечение. При этом линия пересечения двух граней любого геометрического тела, в том числе поверхностей пласти и кромки, а также пластей и кромок с поверхностью торца, называется ребром.
Поэтому щитовая заготовка или деталь вообще не имеют ребер, а только две пласти, четыре кромки и восемь ребер!
Слово "кант", довольно часто используемое нашими мебельщиками на своих сайтах для обозначения кромки или того материала, которым ее облицовывают, в русском языке имеет несколько значений. Это тесьма вязаная или плетеная с вплетенным по ее краю шнуром, узкий цветной шнурок, тканевая оторочка по краю или по шву какого-то швейного изделия, например, одежды, диванной подушки и т. п., а также специальный шнур, вшиваемый в ребро матраца между его пластью и бортом. Согласно определению, кант никак не может использоваться для отделки кромок деталей из древесины и древесных материалов.
Зачем облицовывать кромки?
После того как мы, наконец, договорились о том, что облицовывают кромки заготовок, а не их ребра или в принципе отсутствующие у них канты, следует разобраться, зачем понадобилась эта операция.
С середины 1950-х годов мебельное производство стало превращаться из полукустарного в индустриальное, и высококачественной цельной древесины в Европе оказалось недостаточно. Изделия корпусной мебели стали изготавливать из щитов рамочной конструкции, с двух сторон облицованных клеем и фанерой, с внутренним заполнением из проклеенной стружки, из коротких брусков, из витой стружки, поставленной на ребро, а позже - из древесностружечной плиты, производство которой стало в то время интенсивно развиваться.
Щитовые детали облицовывались тогда со всех сторон натуральным шпоном, а их кромки профилировались. Понятно, что это требовало первоначального оклеивания кромок обкладками из цельной древесины еще до облицовывания пластей - только после этого можно было фрезеровать на них профиль.
Но происшедшее тогда же изменение конструкции массовой корпусной мебели, получившей только плоские кромки, дало возможность использовать для их облицовывания тонкие полосы натурального шпона.
Приклеивание к кромкам щитовых деталей обкладок и наклеивание на них полос шпона производилось с использованием карбамидных клеев в эксцентриковых или винтовых ваймах, в пневмоваймах, а позже - в ваймах с диэлектрическим нагревом, на некоторых предприятиях просуществовавших на некоторых предприятиях до начала 1970-х годов.
Но уже в 1950-х в Германии были созданы двухсторонние кромкооблицовочные станки проходного типа, обеспечивавшие не только наклеивание, но и фрезерование наклеенной обкладки с удалением свесов и профилированием.
Тогда же аналогичное оборудование было создано и в СССР. Но его дальнейшее развитие было остановлено после разработки фирмой Homag в Германии одностороннего кромкооблицовочного станка, впервые продемонстрированного в 1964 году; в этом станке для наклеивания полосы шпона использовался клей-расплав.
Синтетический шпон
В 1960-е годы производство мебели развивалось, полностью перешло на промышленные рельсы, и натурального шпона для облицовывания поверхностей оказалось недостаточно.
Но к этому времени уже были разработаны технологии изготовления его заменителей - смоляных пленок, названных у нас синтетическим шпоном (синтшпоном). По сути это пластик с наполнителем из листовых фоновых (цветных, прокрашенных в массе) бумаг с напечатанным на них рисунком" текстуры древесины. Отличие синтетического шпона от декоративного бумажно-слоистого пластика, представляющего собой гетинакс, в том, что он имеет только один слой листового наполнителя и пропитывается не термореактивными (преимущественно меламиновыми), а термопластичными карбамидными смолами.
Из этих пластиков (синтетического шпона) путем их резки получались и полосы для облицовывания кромок.
Но в дальнейшем в процессе совершенствования технологии производства были получены гибкие рулонные пластики, из которых с помощью продольной резки на так называемых бобинорезательных машинах стали получать рулонные кромочные пластики. При этом конструкция всех кромкооблицовочных станков, выпускавшихся с середины 1970-х до сего дня, была доработана для их применения.
Тогда же было создано и оборудование, позволившее сращивать листы натурального шпона на зубчатый шип по длине. После дублирования флизом полученной ленты, ее продольного раскроя на полосы и намотки в рулон ее также стали использовать для облицовывания кромок на этих станках без предварительного раскроя на полосы заданной длины.
В самом конце 1970-х, в связи с появлением способа "софтформинг", позволившего облицовывать кромки, имеющие постоянный профиль сечения, производителями кромочного пластика специально для его реализации были разработаны материалы, имеющие гибкость не только в продольном, но и в поперечном направлении.
Пластмассовые кромочные пластики
Это название не очень удачно, потому что содержит тавтологию. Ведь пластик и пластмасса - одно и то же.
Правильнее было бы называть их по технологическому признаку экструдированными кромочными пластиками, поскольку их получают именно этим методом.
К ним относятся два вида, различающиеся способом крепления на кромке заготовки: профильные, имеющие по всей длине заершенный гребень, вставляемый в продольный паз, заранее пропиленный в кромке заготовки, и с плоской оборотной поверхностью, наклеиваемые на кромку заготовки.
Первые были разработаны очень давно и активно применялись еще до изобретения синтшпона. Но по ряду причин они получили распространение только там, где требуется очень высокая прочность самой кромки; во всем мире было разработано лишь две-три модели станков для их запрессовки в кромку детали.
Вторые получили распространение примерно с середины 1980-х, когда в Европе был принят стандарт, в соответствии с которым кромки изделий мебели для офисов, общественных зданий и детской мебели должны иметь на ребре фаску или галтель размером не менее 2 мм. Получить ее с использованием тонких пластиков невозможно - после фрезерования вскроется материал плиты-основы. А эти пластики изначально имели увеличенную толщину (до 3 мм), и фрезерование не влияло на качество изделия.
Сегодня, используя и развивая технологии экструдирования пластмасс, изготовители кромочного пластика разработали материалы с различными наполнителями, получившие общее название 3D, т. е. трехкоординатные, или объемные.
Их достоинство в том, что при фрезеровании фаски на ней как бы продолжается текстура древесины, имитация которой нанесена на их лицевую поверхность. Существуют и прозрачные кромочные пластики, в массу которых введена металлизованная фольга, отражающая свет и создающая весьма интересные зрительные эффекты. Существуют и другие кромочные пластики специального назначения, например, перфорированные, используемые как подоблицовочные при обработке кромок деталей из плит с бумажным сотовым заполнением.
В последние годы разработаны новые рулонные кромочные материалы на основе алюминия с подложкой из специальной термопластичной пластмассы. Они могут использоваться там, где требуется высокая стойкость к износу, например, в изделиях кухонной мебели или в жилых автоприцепах. Непосредственно перед облицовыванием кромки слой этой пластмассы расплавляется посредством лазерного луча и выполняет роль клея.
Вся совокупность перечисленных материалов, как использовавшихся ранее, так и применяемых сегодня для облицовывания кромок, - рейки (обкладки) из цельной древесины, полосовой и рулонный натуральный шпон, полосовые и рулонные пластики на основе листового бумажного наполнителя, экструдированные пластмассовые полосы и профили, и т. д. - в отечественной терминологии имеет одно общее наименование - "кромочные материалы".
Более подробно об их особенностях, назначении и применении мы расскажем в следующей статье.
"Фабрика мебели"
декабрь, 2009
Кромочные материалы. Классификация и история (часть 2)
2010.03.19
Облицовывание кромок потребовалось не тогда, когда в мебельном производстве стали широко использовать древесные плитные материалы, а значительно раньше.
Вероятно, еще в начале XVIII века, когда с появлением барокко столяры начали скрывать под тонкой фанерной облицовкой из красного дерева более дешевую хвойную и лиственную древесину, составлявшую основу мебели. При этом приходилось отпиливать от массива дорогой древесины тонкие слои, сожалея о той, которая навсегда уходила в опилки.
Рулонный натуральный шпон
Раньше для облицовывания кромок использовались достаточно толстые обкладки, которые позволяли после фанерования пластей заготовки фрезеровать профиль кромки практически любой сложности. Сначала производится приклеивание обкладок к кромкам, затем - фанерование пластей и снятие свесов облицовки, и только после этого - профилирование обкладки на кромке. Такая последовательность делает клеевой шов между обкладкой и материалом детали совершенно незаметным.
Рост потребления мебели, особенно в послевоенные годы, привел к резкому увеличению спроса на древесину тропических пород. Экономия такой древесины и распространение ДСП как основного материала для производства корпусной мебели привели к необходимости применения для облицовывания кромок узких полос все более тонкого строганого шпона - того же, что и для облицовывания пластей.
Эти полосы обычно получались как своего рода отход или сопутствующий продукт при раскрое кнолей, основная часть которых использовалась для облицовывания пластей. Этот раскрой сначала производился пилением, а позднее, уже в 1960-х годах, с помощью гильотинных ножниц, пришедших в мебельную промышленность из полиграфической.
При этом текстура облицовочного материала на узкой кромке не играла никакой роли. К тому же, и пласть, и кромка мебельной детали при отделке чаще всего подвергались крашению, что устраняло возможное различие оттенков пласти и кромки.
Однако технология получения полос кромочного материала с помощью продольного раскроя кнолей не могла устраивать мебельщиков: длина таких полос не могла превышать 3,5-4,2 м, что при последующем поперечном раскрое по длине приводило к образованию большого количества отходов (немерных остатков).
Когда в конце 1970-х немецкая фирма Kuper разработала линию сращивания короткомерных отрезков шпона по длине на зубчатый шип, производители кромочного материала из натурального шпона получили возможность поставлять его своим заказчикам в рулонах. Тем более, к тому времени изготовители кромкооблицовочных станков уже разработали соответствующее оборудование для его применения.
Промышленная технология изготовления натурального шпона стала выглядеть так:
раскрой кнолей на делянки для облицовывания пластей;
сращивание короткомерных остатков шпона на зубчатый шип по длине в непрерывную ленту с ее намоткой в рулон;
дублирование ленты шпона флизом с использованием клея-расплава;
шлифование лицевой поверхности ленты;
продольный раскрой на полосы заданной ширины на бобинорезательном станке с намоткой полученных полос в рулоны.
Особенности материала
Материал, наиболее часто применяющийся для дублирования шпона, - флиз (нем. Vlies), нетканое термопрессованное полотно на основе синтетических волокон. Его высокая пористость обеспечивает свободное проникновение клея к шпону при последующем наклеивании материала на подложку.
Однако перед продольным сращиванием и дублированием волнистый или неровный шпон должен быть выпрямлен с помощью увлажнения и выдержки пачек в прессе.
Наименьшая толщина дублированного шпона на практике начинается от 0,4 мм, что соответствует техническим характеристикам всех известных кромкооблицовочных станков.
Такая технология увеличивает прочность кромочного материала за счет дублирования, что исключает разлом по слоям, например, из-за недостаточной остроты дисковых ножей при продольном раскрое при пересыхании шпона или при затуплении фрез кромкооблицовочного станка. Предварительное шлифование позволяет отказаться от оснащения этого станка соответствующим суппортом или от применения дополнительного шлифовального оборудования.
Причем дублирование снижает опасность образования на шпоне продольных трещин при поперечном изгибе полосы, например, если шпон будет использоваться для облицовывания профильных кромок методом "софтформинг" или профильных погонажных заготовок. Но шпон, предназначенный для применения в этих технологиях, должен иметь повышенную влажность (около 16%), которая не должна снижаться в процессе его транспортирования и хранения, поэтому на складах необходимо предусмотреть соответствующие климатические условия.
Если же такой материал применяется для облицовывания "перегибистых" профилей, т. е. с профилем сечения, сочетающим несколько идущих подряд чередующихся выпуклых и вогнутых участков, то на его лицевую поверхность в процессе дублирования дополнительно наносится самоклеящаяся пластмассовая лента со слабыми адгезивными свойствами (не оставляющая следов на поверхности изделия), которая удаляется перед отделкой погонажа или кромки.
Рулонный кромочный материал из строганого шпона толщиной 1-3 мм, полученный с использованием сращивания его отрезков на зубчатый шип, не требует дублирования. Считается, что при такой толщине прочность зубчатого соединения вполне допускает изгиб материала с радиусом от 100 до 150 мм - в зависимости от толщины и породы древесины.
Почти маркетри
Внешний вид лицевой поверхности кромочного материала на основе натурального шпона также подвержен влияниям моды.
Так, в конце 1980-х в моду вошла мебель в скандинавском стиле, изготовленная из клееного щита из цельной (массивной) древесины. Но многие производители мебели стали имитировать ее, предлагая покупателю похожую, но изготовленную из ДСП, облицованной сосновым или еловым строганым шпоном. Для того чтобы достичь наивысшей степени имитации, разработали кромочный материал, текстура которого повторяла внешний вид торцового среза щита, склеенного из отдельных брусков, также дублированного и прошлифованного.
Позднее, в конце 1990-х, были выпущены кромочные материалы, имитирующие кромку клееной фанеры, образованную чередующимися слоями волокон древесины с продольным и поперечным направлением, несколько отличающихся друг от друга по опенку.
Шпон для таких кромочных материалов изготавливается по технологии, близкой к той, которая используется для производства шпона типа "файнлайн" (fineline). Слоистые блоки лущеного шпона, часть листов которого подвергается окраске пропиткой, склеивают, впоследствии этот блок строгают на листы требуемой толщины, а полученные листы раскраивают на полосы.
Конечно, стоимость такого материала значительно выше, чем изготовленного с применением более простой первоначальной технологии. Чтобы достичь большей декоративности натурального кромочного материала без значительного увеличения его цены, многие производители наносят различные рисунки на его лицевую поверхность методами пиро-типии, термотиснения и переводной термопечати.
В первом случае полоса прокатывается роликом, нагретым до температуры, достаточной для изменения цвета древесины данной породы. Боковая поверхность ролика имеет соответствующий выпуклый рисунок. При термотиснении обработка производится аналогично, но создается более высокое давление ролика на поверхность древесины, вследствие чего на ней появляется непрерывный узор. Температура этого ролика ниже и не приводит к потемнению древесины. При этом в обоих случаях наблюдается явление термопроката, за счет расплавления лигнина древесины приводящее к припаиванию к ней ворса. Это исключает необходимость в промежуточном шлифовании при последующей лаковой отделке, поэтому рисунок впоследствии не обрабатывается и, соответственно, не повреждается.
Способ термопечати (трансферная, или термопереводная печать) подобен декалькомании и представляет собой перенесение на поверхность изделия многокрасочного рисунка. При этом слои краски в обратном порядке наносят на поверхность термо- и химически стойкой ленты, обычно из полиэтилентерефталата (нейлона, лавсана), под давлением, при температуре 190-220°С.
Ленты с рисунком производятся специализированными фирмами. Изготавливают ленты с однотонными и фантазийными рисунками, имитацией металлических покрытий (позолоты, серебра, бронзы и т. п.), а также текстур древесины любых пород и даже многоцветных рисунков, выполненных в технике маркетри. Причем некоторые из таких кромочных материалов могут служить и раскладками для декорирования пластей мебельных деталей.
Кромочный материал из натуральной древесины с рисунком, заранее нанесенным на него различными способами, особенно актуален при производстве изделий мебели, детали которых не подвергаются крашению в темные цвета, например, облицованных шпоном бука, клена, березы и других пород.
В следующей нашей статье речь пойдет об особенностях синтетических кромочных пластиков с наполнителями из рулонных бумаг и пластмасс.
Фабрика мебели № 1, 2010
Кромочные материалы. Классификация и история (часть 3)
2010.05.06
Пластмассы, называемые также пластическими массами или пластиками, – класс полимерных органических материалов, из которых сегодня изготавливается множество изделий и деталей самого различного назначения.
Большинство используемых пластмасс являются синтетическими. При их производстве органическое вещество с небольшой молекулярной массой (мономер) превращают в полимер, из которого затем получают готовое изделие.
Термопласты и реактопласты
Все пластмассы разделяются на термопласты, которые могут многократно размягчаться при нагревании и снова затвердевать при охлаждении без химических изменений, и реактопласты (термореактивные, или термоотверждающиеся пластмассы), которые можно размягчить нагреванием, но при охлаждении они превращаются в твердые неплавящиеся тела, которые невозможно снова размягчить без химического разложения. Их необратимое затвердевание вызывается химической реакцией сшивки цепей составляющих их молекул.
Для производства пластиков используются самые различные смолы. Среди термопластов наиболее распространены поливинилхлорид, полиэтилен, полиакрилаты, полипропилен и полистирол; среди реактопластов – фенолоформальдегидные, мочевино-формальдегидные, меламиноформальдегидные, алкидные смолы и полиэфиры.
Кроме самого полимера (смолы), в состав пластмасс могут входить наполнители, пластификаторы, понижающие температуру текучести и вязкость, стабилизаторы, замедляющие старение, красители и т. д.
Наполнители полимерных материалов – вещества, которые вводят в состав пластических масс, резины, клеев, лакокрасочных материалов для облегчения их переработки, придания необходимых эксплуатационных свойств (прочностных, электрических, фрикционных и других), а также для удешевления. Наиболее распространенные наполнители – твердые тонкодисперсные продукты, например сажа, двуокись кремния, мел, каолин, тальк, слюда, графит или древесная мука. Применяют также стеклянные, асбестовые и химические волокна. При получении слоистых пластиков роль наполнителей выполняют листовые материалы, например, бумага или ткани, а при получении пенопластов – газы, например, СО2, N2 и летучие углеводороды.
Многослойный меламиновый кромочный пластик
Когда в 1950-х годах в Европе резко увеличилась потребность в корпусной мебели, возник дефицит строганого шпона из древесины твердых пород, используемого для облицовывания пластей. В качестве его замены начали применять однослойные пластики с наполнителем из бумаг с напечатанным рисунком текстуры древесины. Для пропитки бумаги-наполнителя использовались наиболее дешевые карбамидные (мочевино-формальдегидные смолы).
Для того чтобы цвет и текстура материала облицовки пласти и кромки совпадали полностью, кромочный пластик стали нарубать из него с использованием гильотинных ножниц. Однако его толщина не превышала 0,17-0,21 мм, что было недостаточно для приклеивания к кромке с применением клея-расплава на станках, изобретенных для этой цели в середине 1960-х. Кроме того, тонкий кромочный пластик не обладал достаточной прочностью, необходимой при эксплуатации изделия мебели.
Чтобы увеличить толщину кромочного пластика, его стали делать многослойным, используя для пропитки текстурных бумаг термореактивные смолы с неполным отверждением. При этом после пропитки создавался пакет, состоящий из лицевого слоя (пропитанной текстурной бумаги), промежуточного (из непропитанной фибры) и подслоя из бумаги-основы, пропитанной той же смолой.
Собранный из них пакет помещался в пресс, где с помощью давления свыше 20 кг/см2 еще термопластичная смола выдавливалась из наполнителя, выполняя роль клеевого слоя, и при температуре свыше 180°С окончательно отверждалась (полимеризовалась), создавая термореактивный многослойный пластик.
Затем производилось его деление на полосы необходимой ширины, используемые для облицовывания кромок.
Так как для производства этого материала в основном применялись относительно дешевые меламиноформальдегидные (меламиновые) смолы, в Германии кромочные пластики на его основе получили название Melaminharzkante, что в точном переводе означает "кромочный пластик на основе меламиновой смолы", или, для краткости, Melaminkante (меламиновый кромочный пластик). К сожалению, в отечественной промышленности в результате рабского перевода этого немецкого термина была создана совершенно недопустимая калька "кромка-меламин", использование которой сразу выдает непрофессионала.
Многослойный кромочный пластик имеет перед однослойным те преимущества, что обладает большей прочностью и толщиной. Однако у него есть недостатки. Если средний слой при склеивании недостаточно пропитан смолой, при удалении свесов фрезерованием вдоль ребра обрабатываемой заготовки может образовываться бахрома из его неудаленных остатков. Оборотная сторона этого термореактивного пластика должна обязательно подвергаться шерохованию. В противном случае клей-расплав не будет иметь сцепления с зеркально гладкой поверхностью, и вскоре происходит самопроизвольное отклеивание полосы.
В конце 1960-х годов немецкая фирма Held, существующая до сих пор, для производства рулонного пластика создала линию проходного типа на базе разработанного ей двухстороннего ленточного пресса.
Линия включала размоточные устройства для лицевого, среднего и подоблицовочного слоев, ленточный пресс для их склеивания между собой с одновременной полимеризацией смолы, станок для шерохования оборотного слоя пластика и бобинорезательный станок для продольного раскроя полотна в рулон на полосы требуемой ширины с устройством для намотки.
В начале 1970-х годов одна такая линия была закуплена для комбината древесностружечных плит в Подрезково (Московская область), где и проработала до полного износа.
В 1978 году немецкая фирма Hymmen приобрела у фирмы Held лицензию на производство такой линии, а уже в начале 1980-х поставила это оборудование в Подрезково и Электрогорскому мебельному комбинату.
В дальнейшем фирма Hymmen усовершенствовала это оборудование, увеличив его рабочую ширину и мощность ленточного пресса, и сегодня во всем мире по этому принципу изготавливаются практически все пластики типа CPL (англ. continuous pressure laminates – декоративные бумажно-слоистые пластики непрерывного прессования), а также заготовки для ламинированного паркета, где роль среднего слоя играет плита MDF или HPL-древесноволокнистые плиты средней или высокой плотности. Одна из таких линий эксплуатируется сегодня в подмосковном Егорьевске на предприятии Kronospan.
Однослойные пластики с бумажным наполнителем
Первые однослойные полосовые кромочные пластики в СССР производились еще в 1960-х годах на основе листовых пластиков для облицовывания пластей, изготавливавшихся на установках вертикального типа конструкции института Гипродревпром.
Но первые рулонные кромочные пластики с бумажным наполнителем стали изготавливаться только в самом начале 1970-х годов на линии с горизонтальной сушкой полотна, поставленной заводу декоративных пленок московского мебельно-сборочного комбината № 1 в поселке Сходня Московской области немецкой компанией Letron.
Для изготовления пленок для облицовывания пластей предусматривалось использование бумаг массой 60-80 г/м2, а для кромочного пластика – до 120 г/м2.
Комплект оборудования включал также станок для тиснения пор лицевой поверхности полотна будущего кромочного пластика и накатывания на нее защитной липкой пленки. Предполагалось, что она будет не только увеличивать толщину материала, но и оберегать поверхность от повреждений при сборке, хранении и транспортировке изделия к потребителю.
На основе отработанных тогда технологий были созданы отечественные аналоги самого материала – пленки марок РП и РПЭ, а также линия пропитки бумаг модели ЛПРМ-1850, когда-то выпускавшаяся Бахмачским заводом полиграфического машиностроения на Украине.
Однако в конце 1970-х практически полностью отказались от однослойного кромочного пластика на основе бумаг, имевшего лицевую поверхность, полученную тиснением или другим способом, которая имитировала структуру пор древесины. Перестала использоваться и защитная пленка, значительно увеличивавшая стоимость кромочного материала.
Существовал и метод получения кромочных пластиков с высокоглянцевой лицевой поверхностью на основе полиэфирных смол. В процессе получения такой поверхности полотно текстурной бумаги при постоянном движении окуналось в ванну с раствором полиэфирной смолы, после чего сразу же сматывалось в рулон вместе с полотном тонкой полиэтилентерефталатной (лавсановой, майларовой) пленки и выдерживалось там до полного отверждения смолы. Полиэтилентерефталатная пленка обладает высокой химической стойкостью, не вступает в реакцию с полиэфирами и не склеивается с ними, а ее гладкая поверхность после отверждения смолы в бумажном наполнителе обеспечивает получение высокого глянца на его поверхности. Полученная пленка после разматывания рулона подвергается шерохованию с оборотной стороны и разрезается вдоль на полосы необходимой ширины, которые в свою очередь сматываются в рулоны.
Фабрика мебели № 2, 2010
Кромочные материалы. Классификация и история (часть 4)
2010.09.30
При эксплуатации изделия мебели наиболее сильной и интенсивной нагрузке всегда
подвергаются ребра деталей, формируемые кромочным пластиком. Поэтому одно из
самых важных требований к кромочному пластику – высокая прочность как его
самого, так и его сцепления с подложкой, в особенности с пористой поверхностью
кромки древосностружечной плиты.
Одно из неприятных свойств кромочных материалов на основе листовых бумажных наполнителей – высокая хрупкость, что из-за случайных ударов по ребру детали часто приводит образованию трещин и отслоению, в том числе при использовании термореактивных пропиточных смол, отличающихся наибольшей прочностью.
Безбумажные кромочные пластики
Причина высокой ломкости пластиков с листовым бумажным наполнителем – их слоистая структура. В мебельном производстве в основном применяются рулонные кромочные материалы из пластмасс с порошковыми наполнителями, прочность которых значительно выше, чем материалов, произведенных на основе бумажных пленок.
Безбумажные кромочные пластики стали все чаще использоваться в изделиях мебели с середины 1970-х годов, когда кромкооблицовочные станки позволили применять кромочные материалы непосредственно из рулона. Этому способствовало и то, что тогда же при производстве этих пластиков начали использовать технологии нанесения на лицевую поверхность методом термопечати рисунков, достоверно имитирующих текстуры древесины.Такие рулонные кромочные пластики изготавливаются методом экструзии из пластмасс на основе поливинилхлорида (ПВХ), сополимера акрилбутадиенстирола (АБС), полипропилена (ПП), а в последнее десятилетие – и на основе акриловых смол. Толщина этих пластиков составляет от 0,4 до З мм.
Считается, что наименьшую стоимость имеют кромочные материалы из ПП, однако их устойчивость к загрязнению в процессе эксплуатации изделия мебели довольно низкая, Кроме того, недостаток изготовленных из ПП полос – усадка в поперечном направлении после нагрева при наклеивании и следующего за ним охлаждения. При этом оголяется материал плиты вдоль всего ребра детали.
Кромочный материал из ПВХ незначительно дороже, но не устойчив к воздействию УФ-излучения (солнечного света) и со временем меняет цвет. Наилучшими показателями, но и более высокой ценой обладает кромочный пластик на основе АБС.
Появление утолщенных кромочных пластиков из пластмасс было вызвано не только требованиями прочности, но и соображениями безопасности: в конце 1980-х годов в Европе приняты нормы, которые обязывали изготовителей мебели для офиса, общественных зданий и детской выполнять на ребрах деталей фаску размером 2×2 мм или закруглять ее с радиусом не менее 2 мм, Но фрезерование ребер у любых облицованных деталей приводит к вскрытию подложки, поэтому формирование фаски или закругления возможно только на кромочном материале, что и стало причиной увеличения его толщины. Это немедленно выявило общий недостаток любых утолщенных кромочных пластиков из пластмасс с порошковым наполнителем: когда после их наклеивания на кромку заготовки удален свес и на ребре сформирована фаска или закругление, на детали появляется полоса, отличающаяся от пласти и кромки по цвету и текстуре.
Кромочный пластик с эффектом объема
Чтобы избежать этого, производители кромочных пластиков стали делать их не из одноцветной пластмассы, а из материалов как минимум двух цветов – так, чтобы при экструдировании они не до конца смешивались друг с другом и внутри кромочного пластика образовывалась структура, похожая на древесную. Такой кромочный пластик получил общее наименование 3D (3 Dimension) – объемный (трехкоординатный).
Если при производстве таких ЗD-кромочных пластиков используется соответствующая технология экструдирования, они могут иметь внутри несколько разноцветных слоев, параллельных или перпендикулярных пласти. Это позволяет с их помощью имитировать на кромке детали слоистую текстуру среза клееной фанеры или облицовывание двумя слоями разноцветного материала, создающий цветной кант по всему периметру.
Обратная сторона всех пластиков на основе пластмасс с порошковыми наполнителями обязательно подвергается шерохованию для лучшего сцепления с клеем-расплавом, или на нее наносится невидимый слой праймера. Лицевая сторона этих пластиков может подвергаться тиснению или иметь высокий глянец поверхности и для его сохранения дополнительно закрываться липкой лентой, которая удаляется уже у конечного потребителя. В начале нового века большинство изготовителей освоили производство кромочных пластиков типа 3D на основе прозрачных акриловых смол. При экструдировании в их объем могут вводиться пузырьки воздуха, хлопья измельченной металлической фольги, различного рода цветные порошки, другие включения, например, нити, а также плоские полосы фольги, в том числе с напечатанными на ней рисунками, включая имитирующие текстуру древесины.В любом случае на оборотную поверхность прозрачного пластика наносится непрозрачный слой какого-то материала (фольги, пластмассы), исключающий возможность просматривания через него клея-расплава после облицовывания кромки детали.
Эффект металла
Корпусная мебель изготавливается в основном из древесины и древесных материалов, но время от времени возникает мода на отделку и металл. Для этого были специально разработаны кромочные пластики из пластмасс, близких по цвету к имитируемому металлическому сплаву, лицевая поверхность которых облицована фольгой или листовым металлом с матовой, глянцевой или полированной поверхностью, а также с имитацией обработки щетками. Это потребовало создания специальных технологий облицовывания кромок.
Так, в конце 1990-х годов две немецкие компании, IMA и HOMAG, независимо друг от друга разработали технологии облицовывания кромки металлической полосой, которая приклеивалась к облицовываемой кромке заготовки с помощью расплавления лазерным лучом предварительно нанесенного на ее оборотную сторону слоя термопластичной пластмассы. В результате возникла необходимость в рулонном кромочном материале, специально предназначенном для реализации двух этих технологий, – из металла, дублированного пластмассой.
Кромка детали из древесностружечной плиты, облицованная таким способом, отличается высокой прочностью и влагостойкостью. Однако облицовочный материал для него дорог, а оборудование эффективно только на крупных предприятиях и пока не представляет значительного интереса для отечественных производителей мебели.
Отдельное место среди материалов для облицовывания кромок занимают специальные металлические или пластмассовые металлизованные заглушины и промежуточные элементы, предназначенные для заделки торцевых кромок и продольного соединения между собой деталей, одна или две кромки которых облицованы методом "постформинг", Обычно это детали столешниц, двери фасадов и подоконники. Форма и размер этих элементов должны идеально совпадать с профилем кромки, поэтому их поставщиками всегда являются только сами изготовители, заказывающие их у своих субпоставщиков. Особенность заглушин этого вида в том, что они устанавливаются на отлитый вместе с ними заершенный гребень, требующий прорезания в кромке несквозного паза, имеющего точную ширину.
Профили с заершенным гребнем
Для облицовывания кромок существуют и специальные профили, которые начали использовать в производстве мебели из древесностружечной плиты еще раньше, чем смоляные пленки с листовым бумажным наполнителем. Это цельные и пустотелые профили с различным поперечным сечением, имеющие по всей своей длине заершенный гребень, который вставляется в продольный паз, идущий вдоль всей облицовываемой кромки заготовки.
Недостатки таких материалов – необходимость прорезания паза на кромке, трудность состыковывания в углах, проблемы с подбором цвета и текстуры, соответствующих облицовке пласти. Кроме того, свес, образующийся на пласти из-за неточности прорезания паза или из-за разнотолщинности детали, впоследствии не обрабатывается. Это часто приводит к образованию платика (уступа) на пласти, что снижает качество изделия.Однако по сравнению с другими кромочными материалами, которые просто наклеиваются на плоскую кромку детали, эти профили имеют три серьезных преимущества: высокую прочность, возможность получения глубокого профиля на прямолинейной кромке без сложного оборудования, например, станков для облицовывания кромок методом "софтформинг", и возможность формирования профиля на кромках деталей непрямоугольной формы, в том числе на деталях со скругленными углами.
Кромочные материалы сегодня – неотъемлемый элемент корпусной мебели практически всех типов и конструкций, определяющий внешний вид и качество изделия, Рынок предлагает широчайшую номенклатуру таких материалов, при проектировании изделий конструктор не должен руководствоваться только каталогом ближайшего поставщика. Только правильный и удачный подбор кромочных материалов по их характеристикам, цвету и текстурам, практически не увеличивая цены изделия, способен вызвать особый интерес покупателя и способствовать расширению продаж, что особенно важно в сегодняшних непростых для производства условиях.
"Фабрика мебели" № 3, 2010