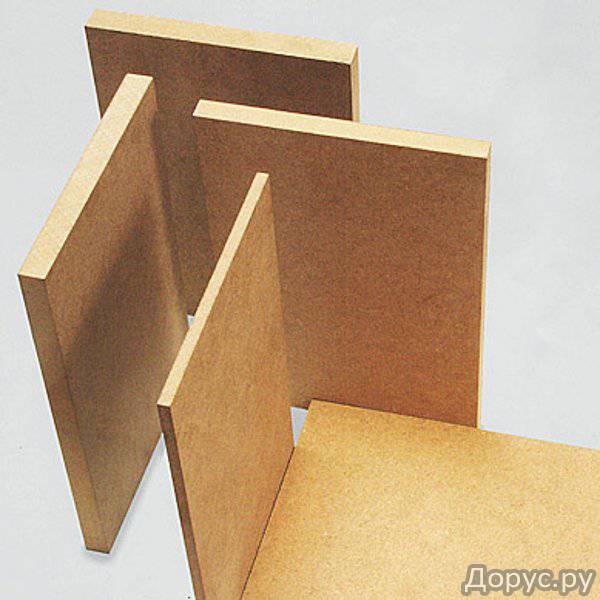
МДФ
Промышленное производство МДФ было начато в США в 1966. В России выпуск был начат только в 1997. Лидером по производству МДФ в мире является Китай.
В процессе производства МДФ можно придавать специальные свойства: огнестойкость, биостойкость, водостойкость. МДФ на порядок дороже ДСтП, тем не менее, использовать материал гораздо выгоднее, ведь МДФ лишена многих недостатков ДСтП: она хорошо «держит» шурупы и не выделяет опасные для здоровья вещества. Кроме того, прочность МДФ в 1,8—2 раза выше прочности древесно-стружечных плит[1].
В основном МДФ используется при производстве мебели, для отделки помещений, например, в виде стеновых панелей, экономпанелей для торговых помещений и ламинированного напольного покрытия (т. н. ламината). МДФ хорошо подходит для изготовления корпусов акустических систем, поскольку он дешев в производстве, имеет однородную структуру и легко обрабатывается. Используется МДФ и для производства тары и коробок для подарков (особенно развито в Китае).
Что такое плиты МДФ?
МДФ(Medium Density Fiberboard) — древесноволокнистая плита средней плотности. Для производства МДФ используется мелкодисперсная фракция древесины, по сути это высушенная древесная пыль. При производстве МДФ в качестве связующего материала используется лигнин, который является натуральным веществом, которое входит с состав древесины. Наличие именно такого связующего и отличает МДФ от других древесностружечных и древесноволокнистых плит, в которых используются формальдегиды. Все это делает МДФ высокоэкологичным продуктом, который в перспективе может занять на рынке как место таких плит как ДСП( ЛДСП) и ДВП.
Этапы производства МДФ таковы: из высушенных волокон древесины, которые обрабатываются специальными лигнином(Лигнин обладает связующими свойствами как уже было сказано выше) формируется ковер. Затем такой ковер под воздействием высоких температур прессуется таким разом, чтобы плотность плиты ( в зависимости от толщины) достигала от 700-870 кг/м куб. Затем готовый длинный лист нарезается на менее крупные листы и остужается до риемлемой температуры. Последним штрихом в этой сложной процедуре является шлифовка плиты, ведь именно она определяет качественность плиты, возможность использования ее при ламинировании, покраске и других работах.
Плиты МДФ используются для:
Изготовление декоративных мебельных фасадов
Предметов для отделки интерьера (стеновых панелей, плинтусов, профилей, столешниц)
Изготовления столярных изделий(дверей, наличников)
Достоинствами плит МДФ являются следующие факторы
Высокое качество;
высокая плотность и однородность плиты МДФ;
отсутствие в составе плиты искусственных химических добавок ;
Экологическая безопасность такой плиты, как следствие неиспользования вредных химических веществ в составе плиты.
Легкость в механической обработке
Высокие звуко- и теплоизоляционные свойства
Возможность нанесения разнообразных декоров, покраски плиты.
Преимущества:
Плиты из МДФ влагостойки, хорошо переносят воздействия влаги, не разбухают, не коробятся.
По механическим характеристикам плиты МДФ превосходят натуральное дерево. Относительно дешевы по отношению к древесине( дешевизна может достигать 60%)
Плита из МДФ особенно часто используют производители фасадов, поскольку только из МДФ можно сделать красивую филенку, закругленные углы.
Плиты из МДФ в отличии от ДСП не так подвержены вредному для изделия из древесины влиянию грибков и различных микроорганизмов, поэтому эти плиты более гигиеничны.
Существуют также плиты ХДФ(High Density Fiberboard, т.е. плита высокой плотности). Изготовление такой плиты идентично изготовлению МДФ, однако используется большее давление, что приводит к более высокой плотности конечного изделия. Плиты ХДФ не отличаются большой толщиной( максимально 3,2 – 4 мм) потому используются на задних стенках шкафов, для отделки интерьеров, при производстве межкомнатных дверей.
ДРЕВЕСНО-ВОЛОКНИСТАЯ ПЛИТА СРЕДНЕЙ ПЛОТНОСТИ
(МДФ, HDF - нем., MDF - Medium Density Fibreboard - англ.)
Экологически чистый материал, так как дополнительное связующее не используется. Им является лигнин, входящий в состав древесины.
Изготавливается путем сухого прессования мелкодисперсной древесной стружки при высокой температуре и давлении. Хорошо обрабатывается.
По влагостойкости и механическим характеристикам превосходит натуральное дерево. МДФ трудно горючая, биостойкая, атмосферостойкая и дешевле дерева.
Применяется в основном для фасадных элементов и корпусов мебели.
Производство и использование MDF
MDF может быть изготовлен из различных целлюлозных материалов. И наиболее важно то, что в производстве MDF может быть использовано вторсырье и не деревопроизводная фибра. Также в производстве MDF используются различные породы мягкой древесины и переработанная бумага, что позволяет варьировать различные свойства конечного материала в зависимости от состава используемых в его производстве компонентов. Комбинации производных дерева и других материалов в производстве MDF позволяют добиться определенных свойств конечного материала: прочность, плотность, влагостойкость.
После появления MDF, этот материал стал широко применяться в различных областях промышленности и в данный момент вытесняет дерево и другие деревопроизводные материалы за счет высоких технических и физических характеристик.
Характеристики MDF
MDF превосходит все конкурирующие материалы по техническим и физическим характеристикам. MDF подвергается тщательной просушке, что резко увеличивает все его физические свойства твердого дерева, т.к. происходит процесс усушки, что спрессовывает структуру материала и повышает валентность второго электронного уровня в связях между молекулами целлюлозы.
Формальдегидные смолы в производстве MDF, в качестве вяжущего вещества обычно используются термоактивные смолы на основе формальдегида, которые в определенной степени являются матрицей для деревянных волоконно-полимерных соединений. Эти смолы выгоднее эпоксидных смол, которые обычно используются в инженерной промышленности тем, что на 75% дешевле, в то же время имеют абсолютно такие же свойства и легче в обработке. Технология соединений при производстве MDF была унаследована из производства ДСП, когда был совершен постепенный переход от практически эксклюзивного использования карбамидных формальдегидных смол к использованию меланин-фориальдегидных смол, фенгол-формальдегида, меланин-карбамид-формальдегида и фенол-карбамид-формальдегида в качестве вяжущих веществ. Меланин-формальдегидные и фенол-формальдегидные смолы показали высочайшие вяжущие свойства, особенно по влагоустойчивости, по сравнению с карбамид-формальдегидными смолами.
Карбамид-формальдегидные, меланин-формальдегидные и фенол-формальдегидные смолы- это конденсатные продукты реакции карбамида, меланина и фенола соответственно с формальдегидом. Эти смолы первоначально растворимые водой, что очень важно при процессе соединения вяжущего вещества и волокна в производстве MDF. Спецификация смол может варьироваться в зависимости от их предполагаемых качеств.
Связывающие соединения Существуют пять способов соединения: механическое соединение, диффузия, электронное соединение, специфическое и химическое ковалентное соединение. Наиболее подходящий способ соединения для применения в дерево-полимерной промышленности – специфическое соединение. В этом соединении используются межмолекулярные и межатомные силы молекул и атомов. Примером таких соединений могут служить соединение Ван Дер Вальса, гидрогенные соединения, и электростатические взаимодействия. Реагируя с водой, карбамид-формальдегидная целлюлоза, выделяет поглощенную смолу, плюс ко всему вода разрывает аминные связи самой смолы. Фенол-формальдегидные смолы имеют более высокую связывающую энергию, чем вода, и, поэтому не так легко выделяются из целлюлозы. Вследствие этого соединения с использованием фенол-формальдегидных смол более влагоустойчивые, чем те, в которых используется карбамид-формальдегидные смолы.
MDF производится с использованием натуральных лигниновых смол, при процессе прессования поддерживается высокий уровень влажности и повышается температура перехода смолы из твердого агрегатного состояния в жидкое, и, диффузия лигниновых смол различных волокон играет важнейшую роль в скреплении волокон.
Меланин-карбамид-формальдегидные и фенол-катбамид-формальдегидные смол сочетают в себе наилучшие вяжущие свойства и влагоустойчивость меланин-формальдегида и фенол-формальдегида с низкой себестоимостью карбамидных смол.
В качестве покрытия MDF, в основном используется пропитанный меланин-формальдегидом бумажный ламинат. Он не подвержен воздействию инородных веществ, не маркий, чрезвычайно крепкий, легок в обработке для повышения уровня различных характеристик, и имеет неограниченную цветовую гамму.
Термическая обработка Уже давно известно, что термообработка – эффективный способ для повышения свойства влагостойкости и прочности материала.
Важными параметрами обработки являются: время и температура, использование воды и химических элементов. Термообработка MDF повышает влагоустойчивость и вяжущие свойства лигниновых смол.
Химическая обработка Обработка формальдегидом проводится с тем, чтобы снизить разбухание волокон MDF, повысить сопротивляемость влаге и улучшить механические характеристики. Химобработка, которая может успешно проводится как при высоких, так и при низких температурах, способна заметно уменьшить содержание влаги в MDF, путем блокировки доступного для проникновения влаги межмолекулярного пространства и изменения химических или физических свойств гидроксильных групп.
Исследования Минато (Minato,1993) показали что MDF, не обработанный формальдегидом, содержит большее количество полимолекулярной воды вследствие термической деструкции вяжущих смол. Поэтому он доступнее для влаги на макромолекулярном уровне.
Другое исследование (Minato et al., 1993) установило тот факт, что степень разбухания волокон и среднее содержание влаги в MDF не обработанном формальдегидом снижается при низкой влажности, но резко повышается при высокой влажности. Это же исследование показало, что сопротивляемость к разбуханию волокон и способность испарения влаги MDF увеличивается при снижении влажности. Прессование с высоким давлением увеличивает прочность MDF, но за счет механических свойств. Процесс прессования включен в производство для того, чтобы разорвать хемиоцеллюлозные и альфацеллюлозный связи, не воздействуя на лигнин (Okamoto et al., 1994).
Напыляемое покрытие Напыление – популярное покрытие, которое используется в промышленности, в основном, для покрытия металла. Это покрытие имеет низкую себестоимость, легко и быстро наносится, имеет полную цветовую гамму, засыхает за несколько минут, чрезвычайно прочно соединяется с металлической поверхностью, наносится равномерно,
Напыляемое покрытие пока еще не имеет коммерческого применения в деревообрабатывающей промышленности. Исследования по поводу применения напыления в данной сфере ведутся в ограниченном количестве. Дешевый, легкий и чистый процесс напыления мог бы быть очень выгоднен в производстве MDF. Дополнительно напыление могло бы повысить свойство влагостойкости MDF.
Дата: 09.03.2010